Corrosion is a major issue that affects industries worldwide. It is a gradual process that can lead to equipment failure, increased maintenance costs, and safety hazards. This article discusses how ThinTech coatings can help prevent corrosion and protect your assets.
Types of Corrosion
There are several types of corrosion, including uniform corrosion, pitting corrosion, and crevice corrosion. Uniform corrosion occurs evenly across a surface, while pitting corrosion creates small pits or holes in a material. Crevice corrosion occurs in confined spaces, such as gaps between two materials.
Uniform corrosion
Uniform corrosion is a type of corrosion that occurs uniformly across the surface of a metal. It is caused by the reaction of the metal with an oxidizing agent, such as oxygen or a corrosive chemical, and is characterized by the loss of metal thickness and weight over time. Uniform corrosion can lead to reduced strength and integrity of the metal, and can eventually cause failure of the structure or equipment. It typically occurs in areas where there is constant exposure to the corrosive agent, such as in pipes, tanks, and vessels used in industrial applications.
Pitting corrosion
Pitting corrosion is a localized form of corrosion that creates small holes, or pits, on a metal surface. It occurs when a small area of metal becomes deprived of oxygen and reacts with a corrosive agent, such as salt or acid. The surrounding metal remains intact, while the pit continues to deepen and spread, ultimately leading to the failure of the material. Pitting corrosion is particularly dangerous as it can be difficult to detect, and can cause sudden and catastrophic failure of equipment or structures.
Crevice corrosion
Crevice corrosion is a localized corrosion that occurs within crevices or gaps between two metal surfaces, such as in overlapping joints, flanges, gaskets, or under deposits of dirt or corrosion products. The corrosion process is often accelerated in these areas because they are shielded from the flow of oxygen or other protective agents, which can create an environment with different chemical and electrochemical conditions than the surrounding area. Crevice corrosion can lead to the formation of pits, cracks, or fissures, which can weaken the structural integrity of the metal and cause leaks, fractures, or failure.
Causes of Corrosion
Corrosion can be caused by several factors, including moisture, chemicals, and oxygen. In the mining industry, exposure to harsh environmental conditions can accelerate the corrosion process.
Prevention Options
Preventing corrosion requires a proactive approach. Coatings, cathodic protection, and proper material selection are effective methods for preventing corrosion. ThinTech coatings are a cost-effective and easy-to-use solution for protecting against harmful elements.
Importance of Regular Inspections and Maintenance
Regular inspections and maintenance are crucial for preventing corrosion. Inspections can identify potential issues before they become severe, allowing for timely repairs or replacements. Maintenance ensures that equipment is functioning correctly and is well-protected against corrosion.
Examples: The Hidden Cost of Corrosion in Mining: How Prevention Can Save Your Assets
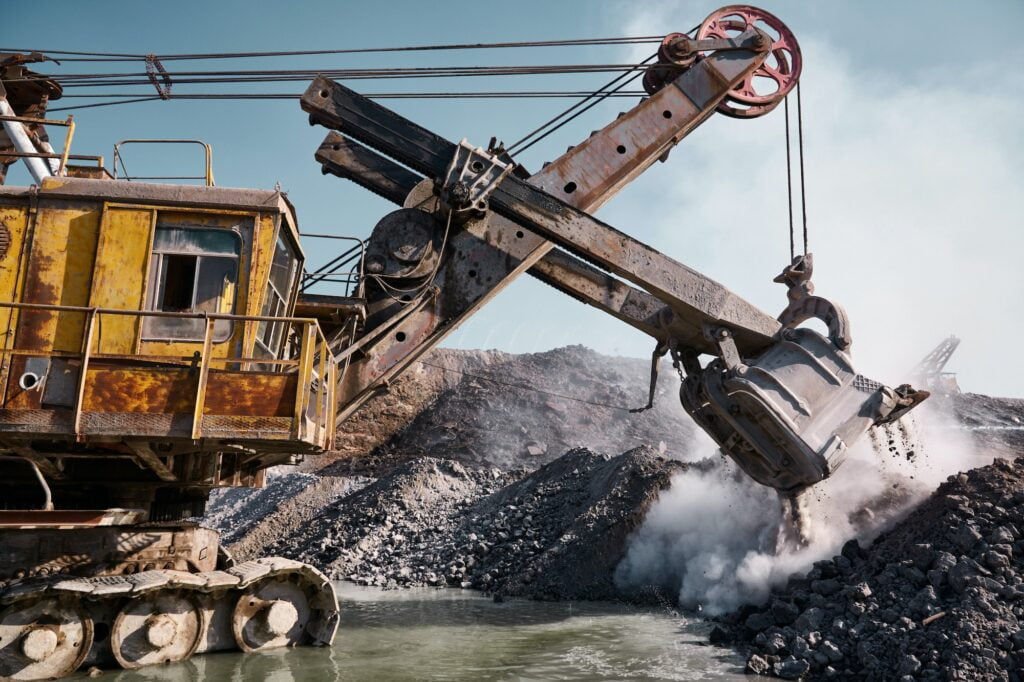
Several industries, including the mining industry, have successfully implemented corrosion prevention strategies using ThinTech coatings:
Corrosion in Mining Equipment
Mining equipment is often subjected to harsh conditions such as exposure to moisture, chemicals, and high temperatures, which can lead to corrosion. Corrosion not only affects the equipment’s appearance but also reduces its lifespan and can lead to equipment failure, resulting in downtime, lost productivity, and increased repair costs.
The mining industry has several types of equipment, such as crushers, conveyors, drilling machines, and storage tanks, all of which are susceptible to corrosion. Corrosion can cause equipment failure, leading to unplanned downtime and increased repair costs, negatively impacting the company’s profitability.
Corrosion prevention measures include using protective coatings, cathodic protection, and proper material selection. Protective coatings, such as ThinTech Metal coatings, form a barrier between the equipment’s surface and the environment, preventing moisture, chemicals, and other harmful elements from causing corrosion. Cathodic protection involves the use of an electrical current to prevent corrosion, and proper material selection ensures that the equipment’s material is suitable for the harsh environment.
Corrosion in Mining Infrastructure
Corrosion in mining infrastructure is a common problem that can cause significant damage and result in costly repairs. Mining facilities typically consist of a variety of structures and equipment, such as pipelines, tanks, conveyors, and buildings, all of which are subject to the damaging effects of corrosion.
The harsh environmental conditions in mining, such as exposure to high humidity, moisture, and salt, can accelerate the corrosion process. Furthermore, the presence of chemicals, such as acids and alkaline solutions, can further exacerbate the problem.
Corrosion in mining infrastructure can lead to a variety of issues, including structural damage, leaks, and equipment failure. In addition to the financial cost of repairing or replacing damaged equipment, corrosion can also cause production downtime, which can result in lost revenue.
Corrosion in Mining Trucks
To prevent corrosion in mining trucks, it is important to use materials that are resistant to corrosion, such as stainless steel or corrosion-resistant alloys. Regular inspections and maintenance can also help to identify and address any corrosion issues before they become serious problems. Coatings and other protective measures can also be used to prevent corrosion and extend the life of mining trucks.
The cost of corrosion in the mining industry is significant, and prevention measures are critical to protecting assets and improving safety. Coatings and cathodic protection are effective prevention options, but proper material selection, regular inspections, and maintenance are also essential. By taking a proactive approach to corrosion prevention, mining companies can save money, reduce downtime, and improve safety.
Conclusion
Corrosion prevention is crucial for the longevity and safety of industrial assets. ThinTech coatings provide a cost-effective and easy-to-use solution for protecting against harmful elements. Regular inspections and maintenance are essential to ensure that equipment is well-protected and functioning correctly.