Introduction
In this Lab study, we examine the reaction and performance of 87% sulphuric acid on coated and uncoated carbon steel specimens. Five specimens, labeled as A, B, C, D and E have been prepared and subjected to a harsh corrosive acid 87% H2SO4 to assess the effectiveness of different applications using ThinTech Metal Coat Gloss. The objective is to evaluate the resistance to corrosion and overall protective capabilities.
Experimental Procedure
(Duration of test 24 hr)
Preparation of Specimens
- Specimen A: Specimen A is a blasted carbon steel sample with no coating.
- Specimen B: Specimen B is a carbon steel sample with surface rust and ThinTech metal coat gloss applied over the top of the existing surface rust at a thickness of 37 microns.
- Specimen C: Specimen C is a blasted carbon steel sample coated DTM with ThinTech metal coat gloss at a thickness of 37 microns.
- Specimen D: Specimen D is a blasted carbon steel sample painted with a 1k industrial paint at 60 microns. No TT coating
- Specimen E: Specimen E is a blasted carbon steel sample coated with a 1k industrial paint at 60 microns with a additional top coat of ThinTech Metal Coat Gloss at 37 microns
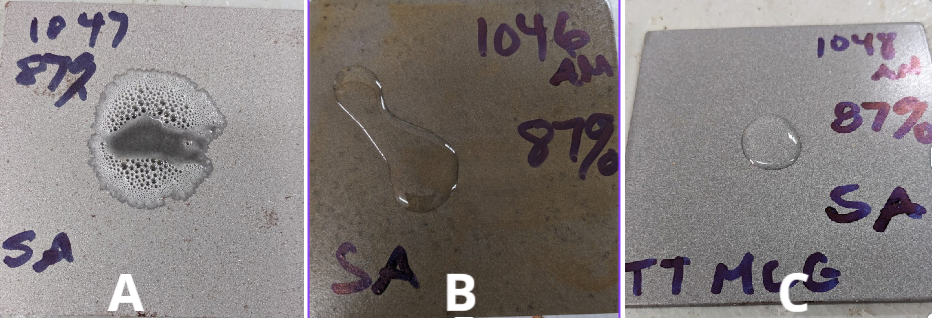
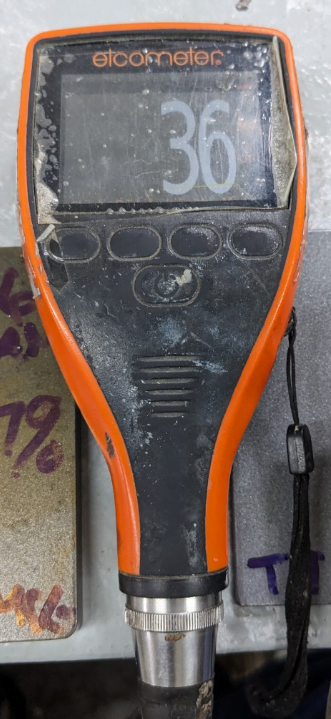
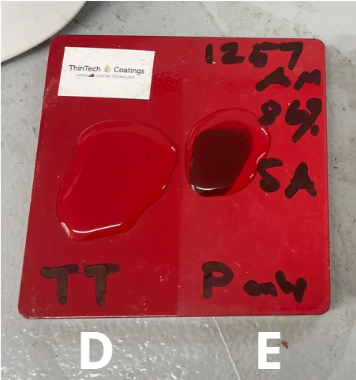
Testing and Evaluation
The five specimens were subjected to a 24 hour spot 87% H2SO4 acid test evaluation to assess their performance in different conditions:
- Corrosion Resistance: Each specimen was exposed to 87% H2SO4, a corrosive acid under controlled lab conditions. The specimens were monitored for any signs of corrosion.
- Visual Inspection: The specimens were visually inspected for any signs of corrosion, blistering, rust, coating degradation, or defects.
- Thickness Measurement: The thickness of the coatings on Specimens B,C,D and E was measured using appropriate calibrated instruments (DFT Elcometer) to ensure they met the specified thickness of 37 microns.
Results
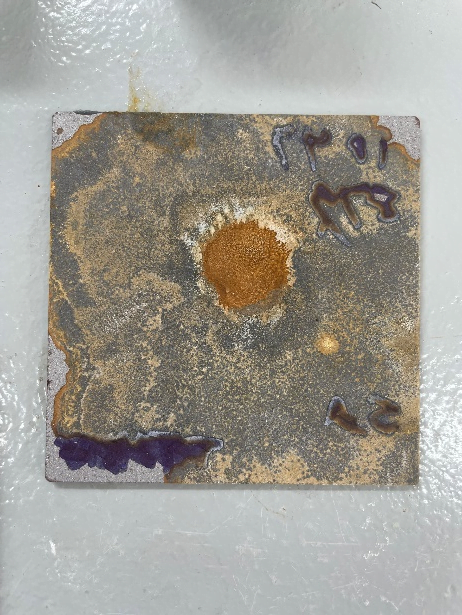
Specimen A (Un Coated)
- Corrosion Resistance: Specimen A exhibited the highest degree of corrosion, with rapid spread reaction, visible chemical reaction formation on the surface after exposure to the corrosive acid.
- Dry Film Thickness Testing: Since Specimen A had no coating, there was no DFT to test.
- Visual Inspection: Specimen A displayed rapid extensive corrosion and surface degradation when compared to the other specimens.
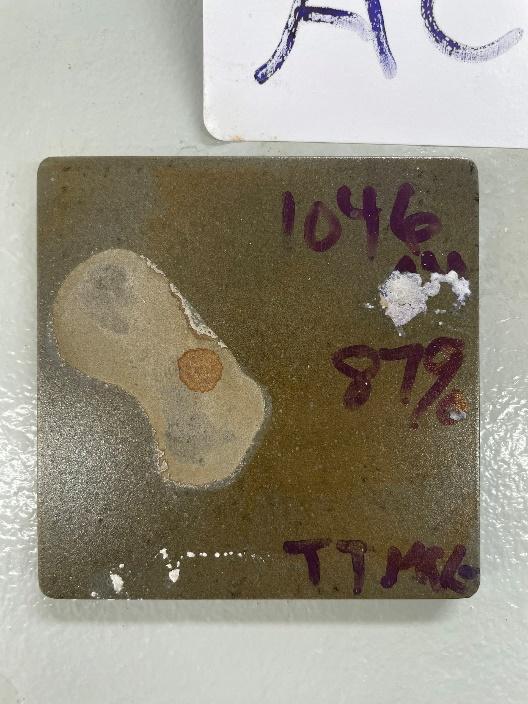
Specimen B (Surface Rust Coated)
- Corrosion Resistance: Specimen B showed improved corrosion resistance compared to Specimen A. Visual damage and corrosion to the coating with blistering. Although some rust was observed, it was less severe.
- Dry Film Thickness Testing: DFT testing revealed that the coating on Specimen B had minimal protection remaining but did hold up well under 12 hours, with minimal detachment.
- Visual Inspection: Some surface corrosion and rust was visible, primarily concentrated around areas with pre-existing rust.
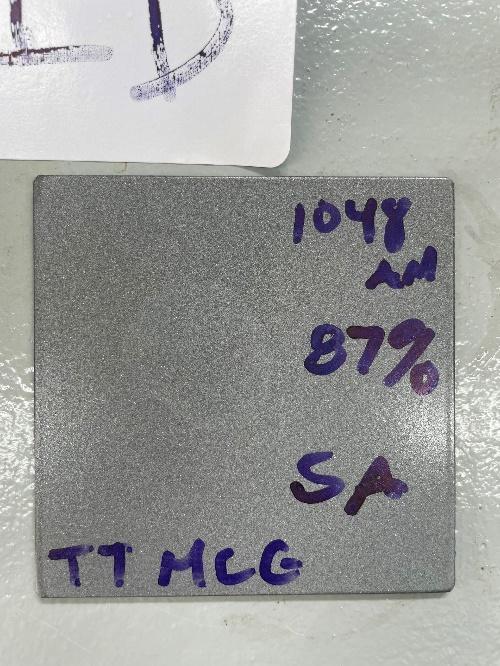
Specimen C (Clean Blasted DTM)
- Corrosion Resistance: Specimen C displayed superior corrosion resistance among the five specimens. No chemical reaction, corrosion or any blistering after exposure .
- Dry Film Thickness Testing: DFT testing indicated excellent film thickness retention shown no loss between the ThinTech metal coat gloss and the blasted steel surface.
- Visual Inspection: Specimen C showed light stain residual from acid but no sign of change to coating or substrate.
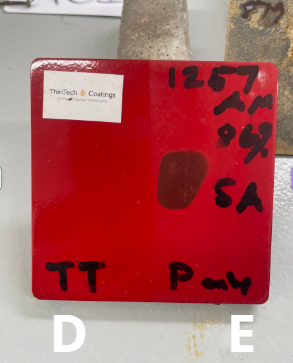
Specimen D (1k Industrial paint)
- Corrosion Resistance: Specimen D exhibited an immediate chemical reaction and turned black, with visible corrosion on the surface after exposure to the H2SO4 acid.
- Dry Film Thickness Testing: DFT testing revealed that the coating on Specimen D had corroded the paint, and started reaction with steel.
- Visual Inspection: Specimen D displayed immediate and extensive damage to the painted surface exposing the steel substrate.
Specimen E (ThinTech Metal Gloss over 1k Industrial paint)
- Corrosion Resistance: Specimen E displayed excellent corrosion resistance among the five specimens. No chemical reaction, corrosion or any blistering after exposure .
- Dry Film Thickness Testing: DFT testing revealed that the coating on Specimen D had corroded the paint, and started reaction with steel.
Conclusion
This Lab study highlights the effectiveness of ThinTech Coating Metal Coat Gloss, the importance of good surface preparation and the high durability to resist strong acids even with a very thin coating application.
Specimen A, lacking any coating, exhibited the poorest corrosion resistance.
Specimen B, coated with ThinTech metal coat gloss at 36 microns with surface rust also provided some protection but was less effective than Specimen C. Ultimately after 24 hours there was noticeable blistering and chemical reaction with the substrate.
Specimen C, which underwent abrasive blasting and was coated with ThinTech Metal coat gloss at 36 microns direct to metal. ThinTech metal coat gloss application, demonstrated superior corrosion resistance and excellent durability even when coated directly to metal.
Specimen D, industrial paint applied directly to blasted carbon steel at 60 micron showed an immediate reaction when the sulfuric acid was introduced to the surface it immediately turned the paint black. Slight penetration through painted surface and slight corrosion to metal substrate.
Specimen E, blasted carbon steel painted with 60 microns of industrial paint then coated with 37 microns of ThinTech metal coat gloss. No visible reaction with sulfuric acid to the coating or substrate.
It is important to note that no chemical change or reaction on the DTM Specimen C which was clean blasted substrate
Painted surface specimen E also performed well using ThinTech Metal Coat gloss as an effective top coat protection enhancement when compared to paint alone.
The results emphasize the importance of proper surface preparation and the choice of ThinTech Coatings will ensure the longevity and protection of painted and un painted carbon steel components in corrosive environments. Furthermore we believe that coating the surface rusted specimen introduced oxides into the coating when applied and contributed to the chemical reaction and degradation of the coating on the rust coated surface.