Advanced Coating Technology
Metal Coating
Available in:

Unlock the Best Deals: Request a Quote Today and Save Big!
Get a quote today for our reliable and affordable coating products. We offer custom pricing based on your specific needs and pride ourselves on high-quality work and exceptional customer service. Contact us now for a personalized quote and all the answers you need to achieve your project.

Need a durable and top-quality metal coating solution for your project? Look no further! Our team offers customized quotes to meet your exact requirements and budget. Our products feature top-of-the-line materials for optimal performance and durability. Fill out our request quote form today to get started!

Fill out our concrete coating request form to protect and enhance your concrete surfaces. Our coatings are durable and come in a variety of colors and finishes, making them ideal for a range of applications. Simply provide your contact information and project details below, and we will send you a personalized quote and coating recommendations promptly. Get started today!
Metal Coating
- Corrosion protection: ThinTech Metal coatings can protect metal surfaces from corrosion caused by exposure to moisture, salt, and other environmental factors. ThinTech Metal coatings help extend the metal surface's life and prevent costly repairs or replacements.
- Improved durability: ThinTech Metal coatings can improve the overall durability of a metal surface, making it more resistant to wear and tear and increasing its longevity.
- Chemical resistance: ThinTech metal coatings provide chemical resistance, protecting the metal surface from damage caused by exposure to acids, solvents, and other chemicals.
- Enhanced appearance: ThinTech Metal coatings can provide an attractive finish to the metal surface, enhancing its appearance and making it more aesthetically pleasing.
- Easy maintenance: ThinTech Metal coatings will make surfaces easier to clean and maintain, reducing the need for frequent cleaning and making it easier to remove dirt, grime, and other contaminants.
Our metal coatings effectively protect and enhance metal surfaces, making them more durable, attractive, and corrosion-resistant. When choosing our solution, metal surfaces can be covered from various environmental and chemical factors, ensuring long-lasting performance and reliability.
Instruction of Use
Surface
ThinTech Metal Coating is the perfect solution for protecting a wide range of metal surfaces, including iron, steel, stainless steel, aluminum, galvanized steel, copper and bronze, powder-coated metals, and painted and primed metals.
Whether you are looking to protect your industrial assets or preserving commercial esthetic, ThinTech Metal Coating offers a durable and long-lasting solution to extend the life of your metal and preserve its appearance. Trust ThinTech Metal Coating to provide the highest level of protection and ensure the longevity of your metal surfaces.
Solution
Our advanced coating technology provides superior protection
- Salt spray,
- Acid rain
- Moisture
- Corrosion, & Rust
- Oxidation
- Galvanic Corrosion
- Wind Drag
- Dirt
- Ice Buildup
- Animal Waste
- Other destructive forces
Characteristics
Appearance: | Clear or available with 20 translucent color stains |
Finish: | Gloss or Satin |
Vehicle Type: | Solvent Base |
Flash Point: | (C Penskey-Martens closed Cup) -9c/15F |
VOC: | Less than 100 g/L |
Weight per Gallon: | 7.36 lb/gallon |
Non-Breathable |
Testing
ASTM D-3359-09 Adhesion Standard test, 300 Hours 4B
ASTM D-3363 Film Hardness Taper, 39.11 average.
ASTM D-2047 Static Coefficient passes ADA requirements*
ASTM D-2803-03 Procedure B (ISO 4623) Corrosion and Filiform. No Filiform or Corrosion 1,000 hours.
E96-10 Water Vapor Transmission, average WVT 0.3473 gr/ft2/hr, average perms 0.8376 gr/ft2/hr.
G155 Xenon Arc, wavelength 340nm irradiance 1.0 w/m2 500 hours, slight change.
ISO 4623 International Standard Corrosion, No Corrosion.
ISO 4628-10, International Standard, Degradation of Coating, No Degradation coated over primer.
*Always obtain independent retest of the static coefficient after applying any coating on walking surface to verify new application meets OSHA requirements.
Spread Rate
Recommended Spread Rate per coat:
- Wet mils: 2.0-2.5 on horizontal surfaces. Vertical surfaces may need wet on tack to avoid runs
- Dry mils: 0.7-1.75
Coverage
640 to 800 sq.ft./gal or 60 to 75 sq.m./4liters (approximate). Coverage will vary depending on the porosity and texture of the surface.
Surface Preparation
For proper adhesion, the surface to be coated must be clean, dry, and in good condition. ThinTech Coatings surface prep or suitable cleaner should be used to remove all oil, dust, grease, dirt, and other contaminants. If scale is present, ThinTech Coatings Scale Remover can be used to remove it, while our Rust Remover is effective at removing light to medium rust. For heavy rust, sandblasting or grinding off the rust is required to ensure proper adhesion of the coating. With ThinTech Coatings, you can trust that your surface will be properly prepared for coating application, ensuring maximum performance and longevity.
To ensure a successful coating application, it is important that the entire surface is free of rust, scale, oil, and grease. ThinTech Coatings recommends wiping the surface with a white rag and solvent to check for any remaining oil and grease. If the rag remains white, the surface is clean, but if it turns dark, continue cleaning until the rag remains white. For hot rolled steel, it is important to sandblast or grind off 100% of the slag to prevent de-lamination of the coating due to surface tension.
After ensuring the surface is properly cleaned, prime the bare metal with a high-quality rust and corrosion primer following the manufacturer’s instructions. Once the primer has dried, apply two coats of ThinTech Metal Coating per the application instructions. It is important to follow the re-application time set by the primer manufacturer to ensure proper bonding with ThinTech Metal Coating. If the re-application window has passed, the surface must be mechanically abraded with a minimum of 600 grit sandpaper to achieve a proper bond for the coating.
For steel or iron surfaces without primer, ThinTech Metal Coating should be applied wet over tack, with no more than 15 minutes between coats to fill micro holes that can lead to rusting. With proper preparation and application, ThinTech Metal Coating provides a durable, long-lasting barrier against rust, corrosion, and other destructive forces, protecting your metal surfaces for years to come.
ThinTech Coatings recommends inspecting the condition of the existing primer and paint to ensure good adhesion and no peeling or chipping. If the existing paint is not in sound condition, it must be abraded off until reaching a solid base or bare steel. ThinTech Coatings suggests sandblasting with Commercial Blast Clean SSPC-SP-6 method or repairing by sanding with 600 grit sandpaper or lower and re-painting as needed.
After any repairs are made and re-painted areas have dried and cured, wipe the surface with ThinTech Coatings Safe Clean to remove any dirt or debris, then wipe down with a damp rag and fresh water to prevent removal of the existing paint. Once the surface is clean and dry, apply a single coat of ThinTech Metal Coating.
With proper surface preparation and application, ThinTech Metal Coating provides a durable barrier against rust, corrosion, and other destructive forces, protecting your metal surfaces for years to come.
ThinTech Coatings recommends thoroughly cleaning the entire surface to ensure a good bond between the surface and ThinTech Metal Coating. Clean the surface of any oil and grease using NanoTech Coatings Surface Prep, then rinse with fresh water and dry to ensure the surface is free of any oil or grease.
To double-check that the surface is free of oil and grease, use a white rag with a solvent and wipe the surface. If the rag remains white, the surface is clean; if the rag turns dark, continue cleaning until it remains white. Once the surface is clean and dry, apply one coat of ThinTech Metal Coating per the application instructions.
ThinTech Metal Coating provides a long-lasting barrier of superior resistance to rust, moisture, corrosion, salt spray, acid rain, UV damage, oxidation, galvanic corrosion, animal & bird waste damage, and reduces ice adhesion. With proper surface preparation and application, ThinTech Metal Coating can protect your metal surfaces for years to come.
For new galvanized steel, it is important to note that it will produce off-gassing for the first several months after plating. It is recommended to allow 6 months for complete off-gassing before applying Metal Coat. In case the age of the galvanized surface is unknown, test a small area for air bubbles or blistering on the surface which will appear in approximately 7 days. If none occur, then the galvanized steel is cured.
Once the surface is determined to be fully cured, clean off all oil, grease, and dirt with ThinTech Coatings Surface Prep. Rinse with fresh water and dry. To ensure the surface is free of oil and grease use a white rag with a solvent and wipe the surface. If the rag remains white, the surface is clean. If the rag turns dark, continue cleaning until it remains white. Once clean, apply Metal Coat following the application instructions provided by ThinTech Coatings. Only one coat should be applied.
To prepare the surface for ThinTech Metal Coating, examine the powder coating for any cracks or damage. If there are any, make sure to have them re-coated or primed with a matching paint to touch up. Next, clean the surface of any dirt, oil, or grease using ThinTech Coatings Surface Prep. Rinse it with fresh water and dry it. Do not use solvents as they can damage the powder coating. After ensuring that the surface is clean and dry, you can apply ThinTech Metal Coating per the application instructions. Only apply one coat.
Application Instructions
Considering the various metals, application methods, and environments, it is recommended to perform a small test on an inconspicuous area with ThinTech Metal Coating to ensure good adhesion and the desired result is achieved. Depending on the type of finish, be it gloss, satin, or mat, there will be a slight improvement in the surface appearance.
To achieve the best finish and appearance, ThinTech Metal Coating is ideally sprayed on. When spraying, ensure that adjacent surfaces are covered to avoid drips or accidental coating. However, in cases where spraying is not possible, alternate methods such as using a fine bristle brush, a high density ultra-smooth foam roller or dipping can be used. Although, this alternate method may not yield the same spread coverage and optimum smooth finish as spraying. If applying ThinTech Metal Coating outdoors, make sure that the ambient temperature is between 45° F and 105° F and the relative humidity (RH) is under 90%. Ensure that there is no chance of rain for at least 5 hours after the estimated completion time of the coating process. It is important to make necessary accommodations for natural elements.
ThinTech Metal Coating should be used with caution, as different finishes and metals require different application methods. Always test ThinTech Metal Coating in an inconspicuous location before applying to ensure adhesion and determine that the desired look is achieved. To ensure a smooth and even finish, always shake the contents thoroughly to re-suspend the nanoparticles that have settled to the bottom. During the application process, make sure to re-shake every 15-20 minutes to re-suspend the settling nanoparticles. When surface preparation is complete and surface is dry and free of dust, begin application using a high volume, low pressure (HVLP) spray gun with a 1.0 – 1.3 size tip and the pressure set at approximately 25 – 30 psi. On a separate piece of cardboard first spray a test pattern to achieve a 6” to 8” elongated pattern approximately 1 1/2” wide in the middle and fluid enough to cover but not puddle. Once the spray pattern is achieved on the test cardboard, spray one coat in a cross-pattern; “left to right” then “up and down”. This will provide sufficient coverage and will help prevent holes in coverage. If applying outdoors, make certain the ambient temperature is between 45° F and 105° F, and RH is under 90%. Make certain that there is no chance of rain for a minimum of 5 hours after the estimated time of completion of the coating process. Make necessary accommodations for natural elements. In addition, if there is high wind, it can affect the quality of the finish as blowing wind can disrupt the spray pattern from your HVLP. It can also contribute to contamination of the finish with blowing dirt. Take necessary precautions against natural elements. (Exception for one coat is on unpainted steel or iron, which requires two coats).
WFT is approximately 2.0 to 2.5 mils on horizontal surfaces. Vertical surfaces may need wet on tack to avoid runs
Ensure that the surface is thoroughly cleaned according to the preparation instructions. Before using, shake the ThinTech Metal Coating container thoroughly to re-suspend the nanoparticles that have settled to the bottom. During application, remember to re-shake the container every 15-20 minutes to ensure that the settling nanoparticles are re-suspended. Pour the coating into a roller pan and saturate a white, ultra-smooth, high-density foam roller (available at most major home improvement stores). Apply the coating quickly in a cross-pattern, starting with “left to right” and then “up and down,” as the coating dries very quickly. Avoid applying too much pressure while using the roller to achieve the best-looking finish. Make sure to work in a well-ventilated area if working in an enclosed space.
To ensure proper application of ThinTech Metal Coating through brushing, it is important to follow the proper steps. Begin by making sure that the surface is clean according to the provided preparation instructions. Thoroughly shake the contents to re-suspend any nanoparticles that may have settled to the bottom. Remember to re-shake the container every 15-20 minutes during the application process to prevent settling.
Choose the appropriate brush size depending on the size of the surface being coated. Use a high-quality bristle brush to apply the ThinTech Metal Coating in a cross-pattern, going “left to right” and then “up and down”. It is important to avoid overworking the coating as it dries quickly. Use light strokes and the tip of the brush to smooth out the coating without pressing down too hard. The desired wet film thickness is about 2.0-2.5 mils.
Always make sure to work in a well-ventilated area and use proper PPE when using ThinTech Metal Coating through brushing to avoid any health risks.
Before starting the application process, make sure that the surface is cleaned as per the preparation instructions. Regularly stir the contents to re-suspend the nanoparticles that have settled at the bottom. Dip the pieces and agitate “back and forth” and “up and down” before moving them to the drying rack. Make sure to re-stir every 15-20 minutes during the application process to re-suspend the settling nanoparticles. Always ensure proper ventilation when working in an enclosed area.
Dry Time
Drying Time (@ 77 F, 50% RH): Drying time is Temperature, humidity and film thickness dependent. (The higher the humidity the faster the dry time
- Touch: 1 hour Through: 2-4 hours Full Cure: 7 Days
Interruption of Work
After the application process, the treated surfaces may not look significantly different from untreated ones. If the application process is interrupted, it’s possible for some areas to remain untreated. In such cases, it is recommended to stop at a corner joint or some other clear demarcation so that the applicator can begin at that point later on. If you need to restart the application process and the last edge that you stopped on has dried, it must be sanded to 220 grit to allow the coating to bond properly at the beginning of the lap joint.
Clean Up
Clean tools and equipment with acetone and flush thoroughly immediately after application is completed and before the product dries. Remember, if the coating dries on the tools, they will not come clean with acetone or any other solvent.
Caution
For safe handling, use OSHA approved 1910.134 and ANSI Z88 2 Respiratory protection. Fresh air and exhaust are required in the work area to prevent inhaling. If inhaled, move to fresh air immediately and call a physician if any physical difficulties occur. Wear butyl-rubber gloves and other skin protection to avoid contact with the skin. If the coating comes in contact with the skin, wash it thoroughly with soap and water. To avoid splashes, use chemical safety goggles or splash shields. Never wear contact lenses without eye protection. In case of contact with the eyes, immediately flush them with water for 15 minutes and seek medical attention. If accidentally swallowed, rinse mouth thoroughly and obtain immediate medical attention. Always make sure to have excessive ventilation when working in an enclosed area.
Care & Maintenance
For routine cleaning, a damp rag or hose can be used to remove most dirt and spills from the surface. While ThinTech’s Metal Coating is resistant to scratches, it is not completely scratch-proof, so it’s important to avoid using abrasive cleansers or scouring pads. If an area is damaged or abraded, simply sand the affected area lightly with 220 grit sandpaper and reapply the Metal Coat. If the substrate is also damaged, make necessary repairs first before reapplying the coating.
Contact Info
- +84 38 8743584
- info@thintechcoatings.com
Safety Data Sheet
Technical Data Sheet
Applications
Superior Surface Protection
Superior Metal Surface Protection.

Corrosion is a primary concern in the oil and gas industry, as it can cause significant damage to equipment and infrastructure, leading to costly repairs, downtime, and potential safety hazards. Therefore, it is essential to take proactive measures to prevent corrosion from occurring.
Superior Concrete Surface Protection.

Exterior building surfaces are exposed to various environmental factors, including moisture, air pollution, and temperature changes, all of which can lead to corrosion and other forms of damage. ThinTech Coating offers a range of specialty nano-coatings designed to protect exterior building surfaces and prevent decay.
Superior Metal Surface Protection.
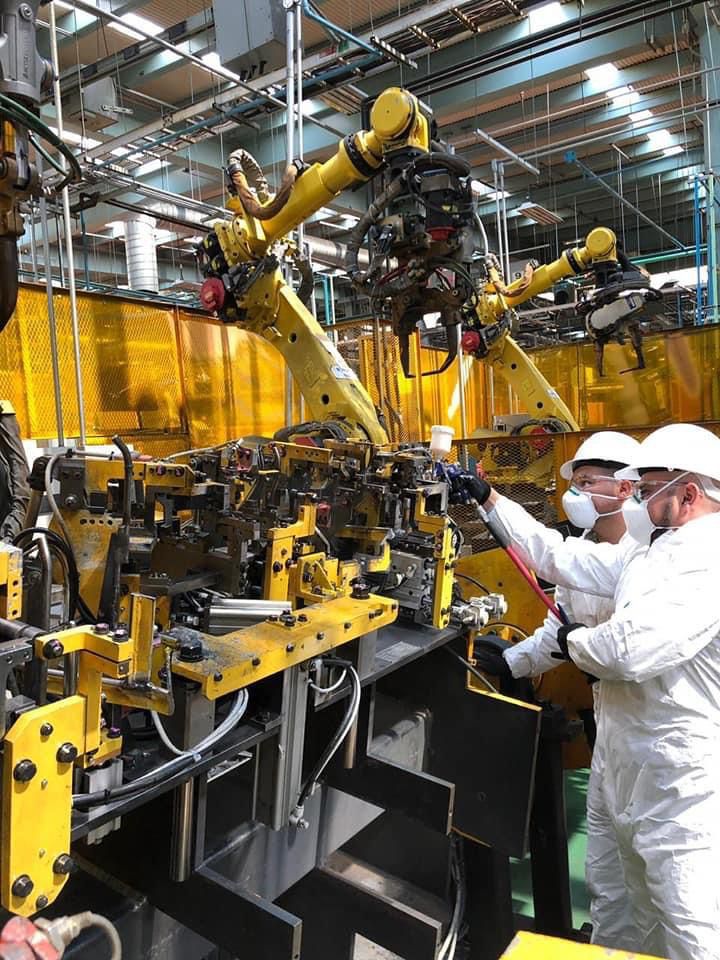
Industrial heavy equipment is often exposed to harsh environments and corrosive substances, which can lead to corrosion, rust, and other forms of damage. ThinTech Coating offers specialty nanocoatings that are designed to protect heavy industrial equipment and prevent corrosion.
Superior Concrete Surface Protection.

Protecting a parking structure’s surface is crucial to ensure its longevity and safety for vehicles and pedestrians. ThinTech nanotechnology coatings offer an ideal solution for preventing corrosion and other forms of damage to parking structures, such as oil stains, chloride, ion exposure, and harsh environmental exposure.
Superior Metal Surface Protection.

Maritime environments can be incredibly harsh, exposing ships and other watercraft to a range of corrosive elements such as saltwater, humidity, and temperature changes. Protecting these surfaces is essential to prevent corrosion and further damage that can compromise the vessel’s or structure’s safety and integrity. ThinTech nanotechnology coatings offer an effective solution for protecting marine surfaces.
Superior Concrete Surface Protection.

Balconies and walkways are exposed to many elements and heavy foot traffic unfortunately these areas suffer from heavy staining and grime buildup. ThinTech concrete coating will provide a deep penetrating natural color enhancing clear nano coating that is impermeable to chemicals and common staining such as oil coffee juices hydraulic fluids diesel fuel and salt exposure. ThinTech concrete coating helps protect and prevent structural exterior and internal corrosion
Superior Concrete Surface Protection.

When it comes to spill containment, you need a product that combines innovation, reliability, and superior performance. That’s where ThinTech Coatings Concrete steps in. Our cutting-edge technology and advanced formulations provide the ultimate protection for your concrete surfaces against spills, leaks, and potential environmental hazards.